The blog section of our web page is to let you know what’s going on at Twisted Willow Fabrication and, when we have permission, to showcase work we have done for our clients. Some may find these blogs very helpful if they have a project in mind. We’ve selected a job we did a few months ago for our first showcase blog because we think the client handled everything perfectly on his end. We pride ourselves on being able to help the client develop a concept and then keep them involved throughout the design and build process. When we pay for custom work, we should get exactly what we want. If you require the services of a fabrication shop, they should take the time to help you with your design concept. They should be interested. They should be grateful for the opportunity. Your vision should matter to them. So how do you go about choosing a fabrication shop, or any other business for that matter? You do what Bill does.
Bill is a client we have recently done work for. We respect the privacy of our clients. Last name and address is withheld. Let me just say Bill knows what he wants. Bill also has a wonderful process when he approaches and deals with a potential company that might do work for him. We think Bill might be able to help others, the reason we have asked him if we can showcase his job. Bill contacted us through Messenger on our Facebook page. His approach was wonderful. He first described an area on his property and gave me a loose idea on how he wanted to treat it. He finished his message with, “could we start a conversation about how your business could be a good fit for me?” My first impression was wow, good form. A perfect 10. I scheduled a time we could meet and we had a conversation and exchanged ideas. Bill has recently had a beautiful concrete driveway installed. It’s bordered with washed stone on one side, garden area on the other. Bill wanted something that looks nice and original to define these areas.
Now remember, Bill knows what he wants, but he’s open to ideas. Bill did not start out telling me what he wanted. He wanted to see what I came up with. Another perfect move. The first thing we do is to make sure the client gets what he/she needs, even if it doesn’t involve our services. We always throw out all sorts of ideas. Brick or Pavers like many people do? No, that’s not what he was looking for. Don’t even mention a plastic landscape border to Bill. Bill hates plastic. Bill wanted steel. We can do that. Not knowing what Bill knows (Bill knows what he wants), I start by throwing loose ideas of how we could handle this, trying to reel in some of Bill’s ideas. That’s when Bill showed me his cards.
One of Bill’s favorite artists uses Cor-Ten. Now I should say Cor-Ten (aka Corten, Cor-10) is a registered trademark of U.S. Steel. We won’t be using that name again because it’s registered and we didn’t use that brand name. Cor-Ten (last time I’ll use it, I promise) is a weathering steel. Weathering steel is designed to be used untreated. Oxidation that forms on it (rust) seals the surface and impedes further oxidation. Oxidation (rust) is the protective surface. Weathering steel plate goes by the International Standards designation ASTM A588. Those walkways and bridges over roads and expressways that are dark brown and a little rusty looking are likely made out of weathering steel. It’s used quite a bit in art and architecture. It’s an interesting alloy. Not so interesting to work with. It’s a very hard steel alloy. For other fabricators interested in working with weathering steel, you’ll need to reduce your plasma cut speeds by 20 to 25%. It reminds me of AR plate.
Once I knew what Bill was really interested in, I did what I usually do. I pushed a little to get the potential client out of his box. At the time I didn’t know Bill doesn’t live in a box. Bill knows what he wants. BUT…..I normally challenge the potential client to think a little crazy. Just think a little crazy with their (his) design. We don’t have to use crazy, but we can reel the crazy thoughts in later and, as I have found in the past, get the client a design they really love. So Bill played along. We talked crazy on possibilities. I modeled a potential design we discussed. But Bill knows what he wants. He went back to his original idea after we discussed the model. We both knew that was the design. My next step was to research A588 weathering steel. What process do I use to weld this stuff? What’s the best shielding gas? It turns out I had everything I needed. My main supplier had A588 and gave me a price. It was go-time. I gave Bill an estimate. I asked him to get other quotes as well. I don’t know if he did, but a week later Bill gave TWF the job, even though he knew we had never worked with A588 before. TWF was not going to let him down.
Bill’s job required around 80 feet of A588, 4 inches wide, ¼ inch thick and 12 foot long sections. Each section had opposing machined lap joints on each end. This was for strength when attaching each section to create a border that looked like one piece. Stainless steel binding posts were used to join the machined ends together. The binding posts were used for a clean look, but also to create a breakaway in case something like a snow plow hit the border. Stainless steel 8” spikes and mounting plates were fabricated and driven into the ground to mount the A588 border sections, washed stone between the border sections and concrete driveway pad. The A588 driveway border mounts were attached to the stainless ground mounts with stainless steel bolts, securing them in place. The ends of the A588 border were treated with a “gentle slope”.
A few weeks after the installation, I checked to make sure Bill was satisfied with the job. I will return at least once to make sure the A588 is taking on the finish we expect.
We don’t leave Bill with a custom job that he has to worry about in any way. Twisted Willow Fabrication supports the work we do. We have a complete record of Bill’s job, including CNC cut programs. We know the hardware, materials and processes used to create Bill’s custom job. If anything happens to Bill’s driveway border, even if it’s many years from now, we’re just a call away. It can be repaired.
Thank you, Bill, for trusting us with your vision.
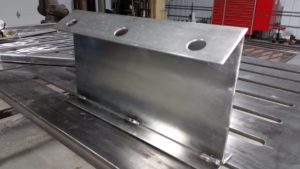
The model built for Bill, to be used with low voltage LED rope lighting.
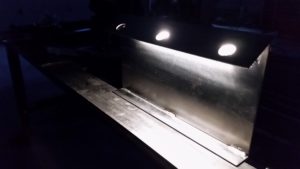
Model with lighting.
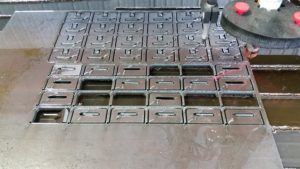
CNC plasma cutting the mounting hardware.

Mounting hardware pieces.
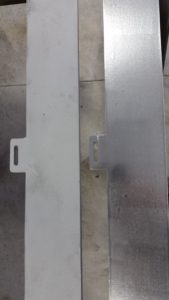
The border pieces. The left side has just been sandblasted, the right side burnished.

“Weathering” the weathering steel outside.

Installing the border. More stone to be added after installation.
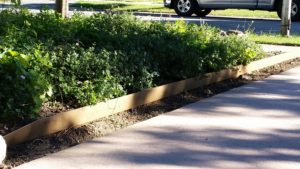
Installing the border. Stone to be added.
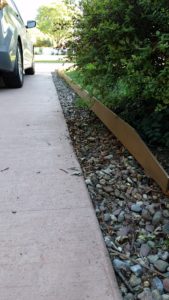
A look down the driveway to the bend. The “gentle slope” on the end. More stone will be added.